Rolls-Royce is to provide the main propulsion system and propulsion control system for the 158-metre ferry ordered by Danish operator Mols-Linien at Finnish shipyard Rauma Marine Constructions (RMC).
Rolls-Royce will deliver two Promas system units, each integrating a controllable pitch propeller, propeller hub cap, and a rudder with bulb and a twisted leading edge into one hydro-dynamically optimized unit.
Gearboxes, steering gears, two tunnel thrusters in the bow and a control system are also part of the delivery.
Gary Nutter, Rolls-Royce, Director Products, said: “By adapting the propeller and rudder into one propulsive unit, Promas offers increased propulsive efficiency and improved manoeuvrability. It is chosen by both conventional single and twin screw ships, such as the passenger ferry to be constructed for Mols-Linien.”
Cavitations tests will be carried out at the advanced facilities of the Rolls-Royce Hydrodynamic Research Center (HRC) in Kristinehamn, Sweden. where the performance of the combined propeller and rudder system (Promas) will be tested prior to manufacturing.
Göran Grunditz, Rolls-Royce, Manager HRC, said: “Cavitation tests are digitally documented and log efficiency, cavitation performance and risk of cavitation erosion on the equipment. The tests provide us, the yard and the owner with useful data related to estimated future fuel consumption and can also help the owner when planning for future services intervals.”
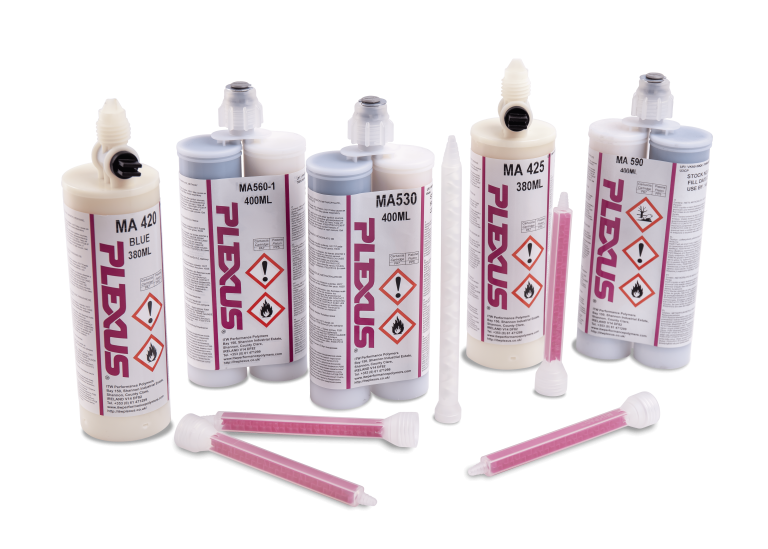
Vaber Industriale Announces RINA Certification for ITW Plexus Structural Adhesives
ITW Plexus MA420, MA425, MA530 and MA560 structural adhesives, distributed by Vaber