Contrary to common belief, boat tanks are not accessories but active, essential parts of the vessel. The system is made up of the container (fuel tank), sampling connections (suction pipes), vent connections, loading mouth, control valves (E.P.A. regulations), Level Sensor For Marine Tanks connection, tightening point through pipe clamps, connections to the filter, fuel pump, and so on.
The fuel tank is located inside the hull of the boat and not on the outside; thus, any leaks can’t be released outside. This presents a significant boat safety risk because, if a leak occurs anywhere in the system, a failure is very likely to occur. A big surface producing steam in a restrained and unventilated space can cause an explosion, for example by simply starting the engine or activating (even automatically) a bilge pump (just to name one of many electrical devices aboard).
HOW TO CHOOSE THE IDEAL TANK
One must choose a tank wisely before installing it on board; for this reason, knowing the advantages and disadvantages of each type of tank on the market is essential. For example:
- Plastic tanks – which are mainly made of polyethylene, Eltex, PVC, etc. – are cheap, but they are only a good option with small measures, generally for portable tanks.
- Aluminium tanks, which can be easily manufactured, require the appropriate equipment and entail high costs during production. Furthermore, their thickness should be at least 6/7 mm, and they are more exposed to corrosion.
- Stainless steel tanks tend to have a limited lifespan that depends on three factors:
- The workmanship, which lies in the choice of the materials (as the steel sheet should be certified as true 316l low carbon stainless steel), in the quality of the weld joints (in that they must be professionally TIG welded), and the process of passivation of the weld (which, through the use of certain chemical agents, restores the surface and makes it stainless again).
- Any galvanic currents, which tend to attack the most sensitive areas, i.e., those where the welding has been carried out. The migration of the nickel in the alloy is responsible for the creation of a very thin, invisible veil of nickel oxide that protects them from corrosion.
- The geometry and conditions of use, because large surfaces tend to generate significant forces that can be even greater when the vessel is in a very rough sea. Indeed, in this case, the weld joints may represent points of failure due to the hardening of the material and the stress applied to the sheet metal exposed to the sloshing process.
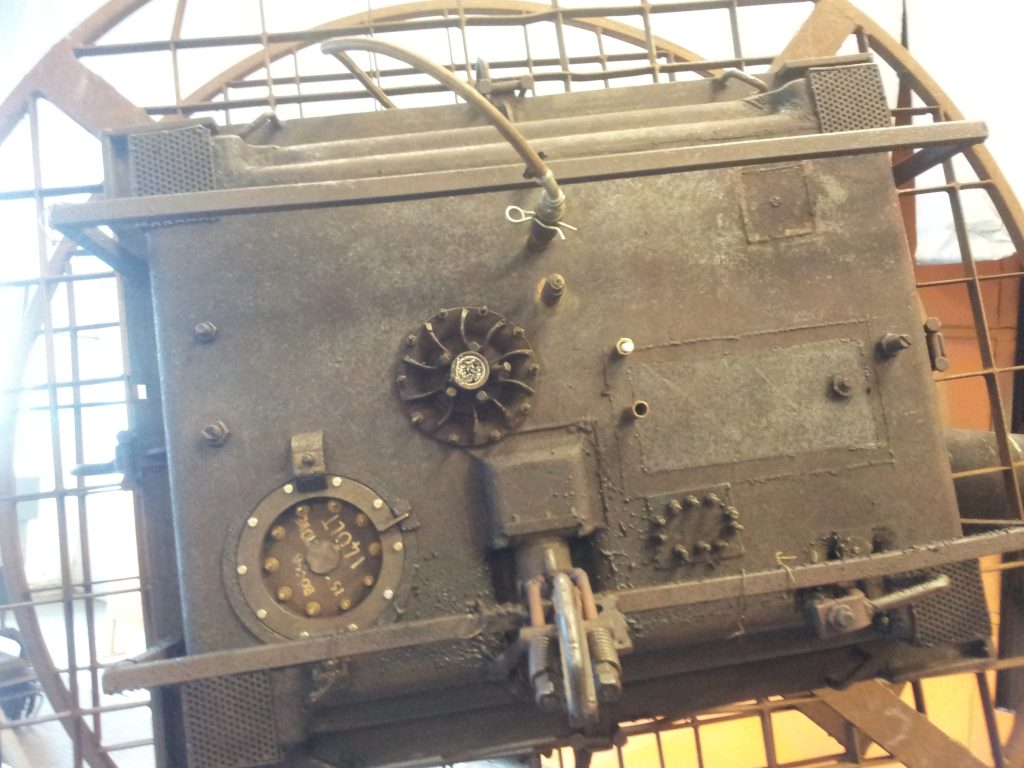
CROSS-POLYMER TANKS
In comparison to stainless steel, plastic, or aluminium tanks, the cross-linked polymer ones present superior mechanical and chemical features. The force applied to the surface is the result of the pressure applied on a more or less extended area: F=PxS (where F is the force, P is the pressure, S is the surface). In the case of a tank with the upper side measuring 1 sq.m (i.e., 100 cm x 100 cm = 10,000 cm²), F=0.1 (Kg/cm²) x 10,000 (cm²) = 1,000 Kg. Thus, with just 0.1 atmospheres, enormous forces can be generated.
These special tanks offer other advantages:
- A superior mechanical module in order to withstand written efforts (some tanks can reach 5 sq.m of surface on just one side).
- A certified chemical barrier that withstands the migration of the hydrocarbon through the molecular mesh of the polymer (fuel tank safety concerns).
- An excellent elastic module at low temperatures (normal polyethylene weakens when at low temperatures).
- Manufacturing techniques for the inserts that, during the moulding process, must guarantee the hermetic sealing for the passage of the fuel.
- Correct design of the geometries, in order to reduce efforts.
- Professional moulding, that must guarantee the cross-linking process in the case of special polymers.
- International regulations that, by establishing all these measures, impose that if a shipyard wants to export its products to the United States, it MUST have aboard all the components in compliance with these laws.
PEROXIDES DURING CHEMICAL REACTION
Twenty years ago, SIC DIVISIONE ELETTRONICA chose to rely on the best polymers, which use peroxides during chemical reaction, in order to obtain a cross-linked moulding as a whole. Indeed, the hydrogen ties all the high molecular weight chains (basic polymer): this process strongly increases the mechanical module and, at the same time, both enhances the elastic modulus at very low temperatures and strengthens the barrier, hindering fuel to penetrate the walls.
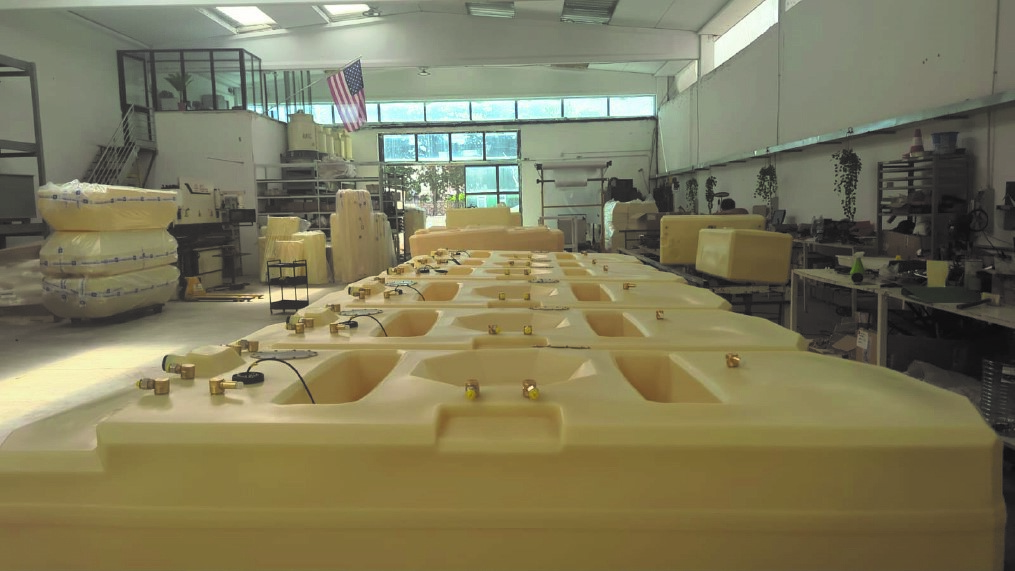
ALWAYS IN COMPLIANCE WITH THE MARKET
All the items manufactured by SIC DIVISIONE ELETTRONICA respect the international laws ISO 21487, ISO 10088, ISO 8099 and ABYC/NMMA/EPA/CARB, etc. Furthermore, its manufacturing techniques provide the market with high-quality components and satisfy the new low permeability standards that were introduced with the EPA/CARB laws on January 1st, 2011. A wide range of SIC’s tanks are also in compliance with the standards established by the American Coast Guard and the ABYC.
Moreover, with its forty years of experience in several areas – such as electronics, mechanics and chemistry – SIC DIVISIONE ELETTRONICA is a leader company in the design, patenting, and production of:
- Its own special brass inserts that optimize hydraulic and mechanical seals.
- Capacitive Level Sensor For Marine Tanks that guarantee precise and continuous level measurements.
- Special polymers for different applications, such as for double or triple wall water tanks with special pure silver fillers, or for nano-filled polymers tanks with the aim of obtaining particular specifications.
SIC DIVISIONE ELETTRONICA is also able to modify some processes in order to create innovative recipes and to manufacture custom moulds in its internal departments.
EXPORTING TO AMERICA
Exporting to the American market means having to comply with its mandatory laws that regulate the use of many components, such as fuel tanks on recreational boats. In fact, the American E.P.A. (Environmental Protection Agency) requires particular technological precautions to be adopted when installing those components.
More specifically, tanks should always:
- Face with a daily permeability limit, because the polymer has to be lower than 1.5 g x 1 sq.m when the temperature is 20°C.
- Withstand low temperatures and severe crashes.
- Withstand internal pressures that tend to push on the surface.
- Withstand fire exposure for several minutes, even with gasoline inside.
- Not have any openings apart from those located on the top surface.
- Display data regarding the polymer and the temperatures to which it can be exposed.
Unfortunately, a lot of shipyards find themselves in unpleasant situations when they export uncertified vessels to America, as their goods are stopped at the borders and they have to face expensive costs to ship the goods back to the country of origin.
SIC DIVISIONE ELETTRONICA already offers free design studies to all shipyards that want to comply to safe export to America and, shortly, to the new European market as well. New European laws are currently under approval by the entire Community. For this reason, it is very important that both the tanks and all the systems in the boat are previously well designed and applied, ensuring boat safety compliance when the laws will be officially approved.