The sustainability parameter to judge manufacturers is the carbon footprint of their products, whether composite or any other material. It can be very complex to calculate this for overall processes, given the contributions of different components, supply chains, shipping, and energy consumption at each stage. The need to reduce the environmental impact of the marine industry, especially of GFRP hulls, has been a topical issue in recent years.
Production systems are now less polluting thanks to the diffusion of new technologies and use of less polluting resins, but much remains to be done to dispose of boats and molds at the end of the life cycle. The future of boating is in the environmental compatibility in the different phases of construction, in relation to the economic and ecological aspects. Research aimed at solving the problem in this industrial sector is under way.
TYPES OF COMPOSITES
One of the main reasons for choosing composites in boat construction is to overcome corrosion problems and reduce the weight of boats. Most structural Marine Composites employ E-glass fibers in an unsaturated polyester resin matrix (GFRP).
Where higher stiffness is required, carbon fiber reinforced epoxy resin is used (CFRP). Composites based on these thermosetting resins are not easy to recycle; composites based on thermoplastic resins, on the other hand, can be recycled with relative ease, but their use in boat building is not widespread yet.
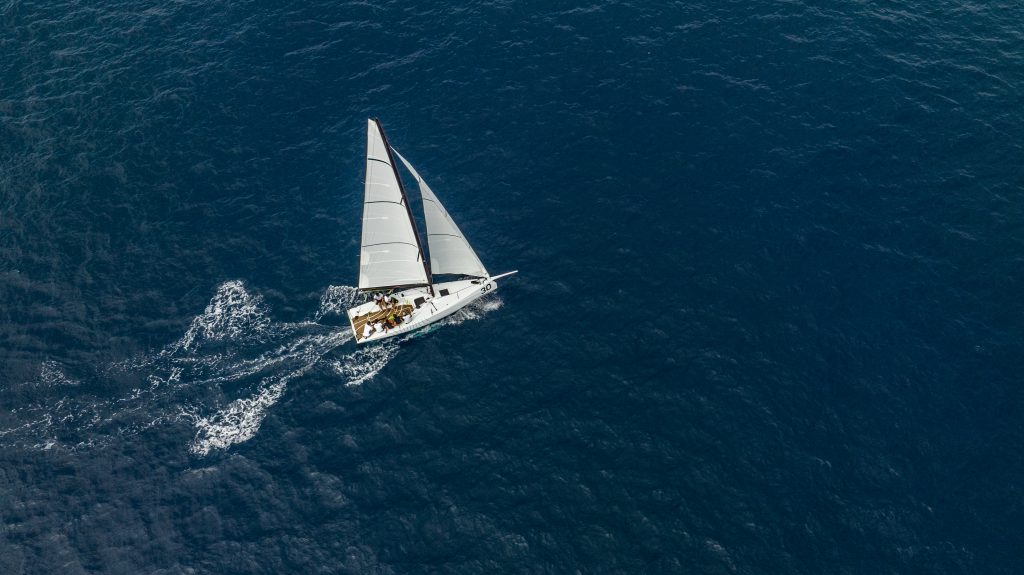
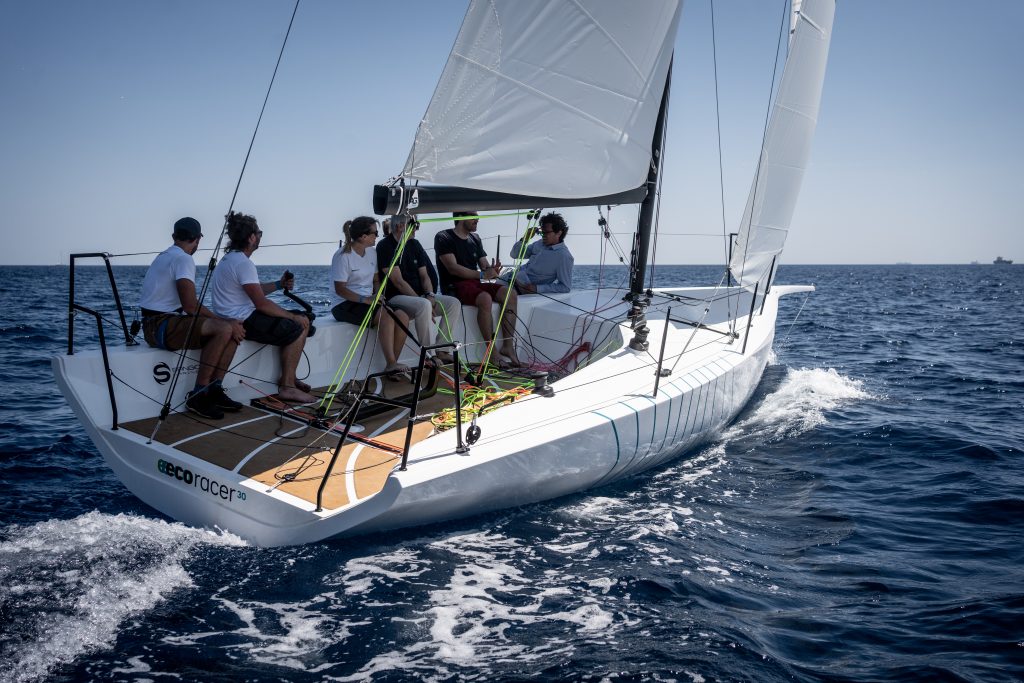
FIBERGLASS’ END OF LIFE
As emphasized by the International Maritime Organization and the European Boating Industry, fiberglass boats have a lifespan of 40 years, which has contributed to the limited attention given to end-of-life disposal until now: many early-produced glass-fiber boats are still in use.
However, soon these boats will reach the end of their operational lives and it will represent a large and complex problem: currently, it is estimated that approximately 95% of fiberglass boats end up abandoned at the end of their lifecycle.
Projections indicate that the number of boats reaching their end-of-life in the European Union is expected to exceed 30,000 boats per year by 2030. Consequently, an average of over 23,100 tons of end-of-life composite waste will be generated annually. However, this value would be much lower than the end-of-life management costs of the ‘old boats’ product or other similar products in terms of complexity, particularly due to the nature of its majority component, the FRP – Fiberglass Reinforced Plastic.
The FRP is not easily recycled, not in its physical form, because its component materials are very difficult to separate and almost impossible to re-utilize into a new work cycle with other products. The main issue is to find the best balance between environmental and economic costs. This makes Fiberglass Recycling a crucial topic in the industry.
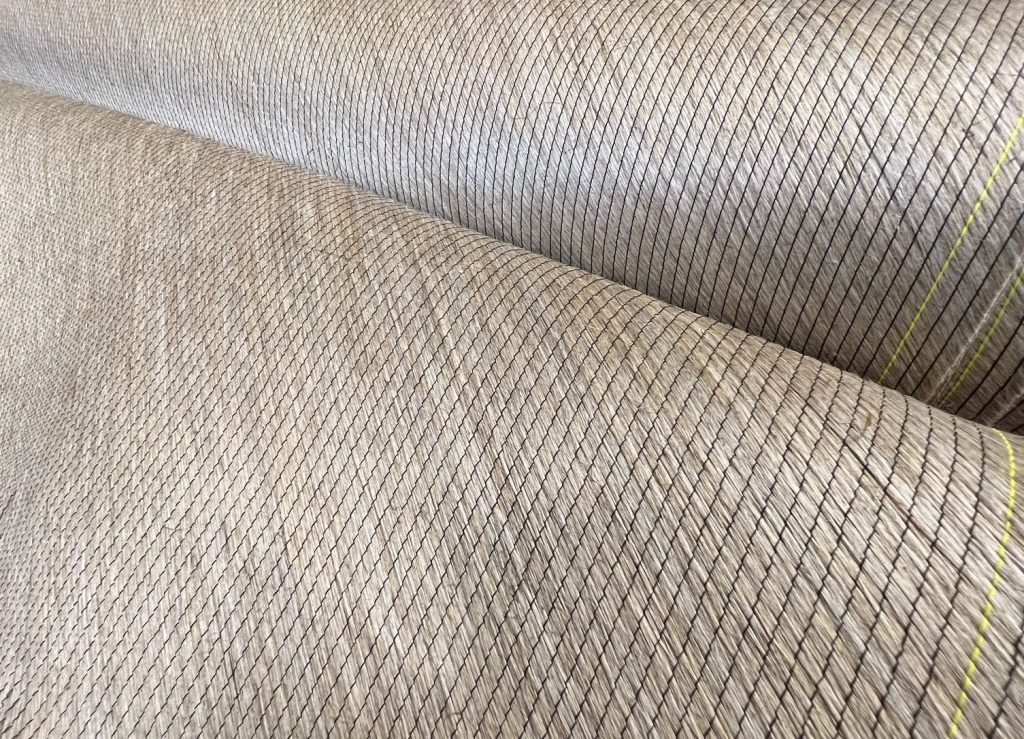
BIOCOMPOSITES
The ever-growing interest in the environment and sustainability issues is pushing the market in general, and the marine sector in particular, to seek ways to replace conventional synthetic fiber (and resin) composites with bio-based composites. Industry and research are looking for ecological, reusable, and recyclable materials.
Biocomposites are attracting a lot of attention because not only can they provide materials with excellent properties, but they are easily recycled or disposed of at the end of the product’s life. The main advantages of biocomposites are high specific resistance, high sanitary safety, CO2 neutrality, good damping properties, thermal insulation, high sound insulation, low density, lower production energy, and lightness.
A recent survey states that the global biocomposites market has achieved an annual growth rate of 11.8% from 2016 to 2024 (source: marketsandmarkets). Market size is expected to reach $10.89 billion by 2024.
- RECYCLING means that the end-of-life (EoL) component or production waste becomes a new product or material with a different use. This requires energy and other resources to convert waste into something else. The economic feasibility and environmental impact of these recovery processes are yet to be verified. Generally speaking, the material circularity with a 100% closed cycle (‘Cradle-to-Cradle’ recycling) is a possible objective with composite materials, although the economic feasibility and environmental impact of these precursor recovery processes must be verified.
- RECOVERING means transforming waste into fuel or thermal energy after removing all the individual components that can be reused.
- DISPOSAL means the elimination of waste in landfill or incinerators. These are the most widely used but less recommended treatment methods, because there is no recovery of material or energy. However, let us not forget that the cost-effectiveness of recycling also involves: A rethinking of the design process, aimed at the design of new products, which takes into account their disassembly at the end of their life; A reorganization of demolition operations, which exploit robotisation to reduce the interventions of unqualified personnel in processes, such as cutting the hull. Both are demanding in terms of human resources, and risky for the workers in terms of safety.
NATURAL FIBERS
Natural fibers are relatively new to the production of industrial composites. A natural fiber is one obtained from a material that grows naturally: hemp, flax, and wood can be used.
The Nova-Institute reported the carbon footprint of natural fibers between 0.3 and 0.5 kg of CO2eq per kg of fiber. The mechanical properties of natural fiber-based composites are different from those of the other fibers, but they are still extraordinarily strong, stiff, and lightweight relative to their density. An example: flax is available in continuous form, preferred for pultrusion, as the individual filaments are long enough to withstand the tensile stress necessary in producing a profile.
Use and development in the industry, such as Volvo’s collaboration with a sustainable lightweight company and flax fiber supplier Bcomp, suggest that this natural fiber may be a legitimate future option for composite solution providers. Clearly, the path to sustainability and carbon neutrality is not an easy one for the composites industry.
While the rise of natural fibers is welcome and represents an area of notable progress, carbon and glass fibers still perform better and have more established and optimized manufacturing processes. At the heart of sustainability assessments is the durability calculation: how will the final product affect emissions over decades of use?
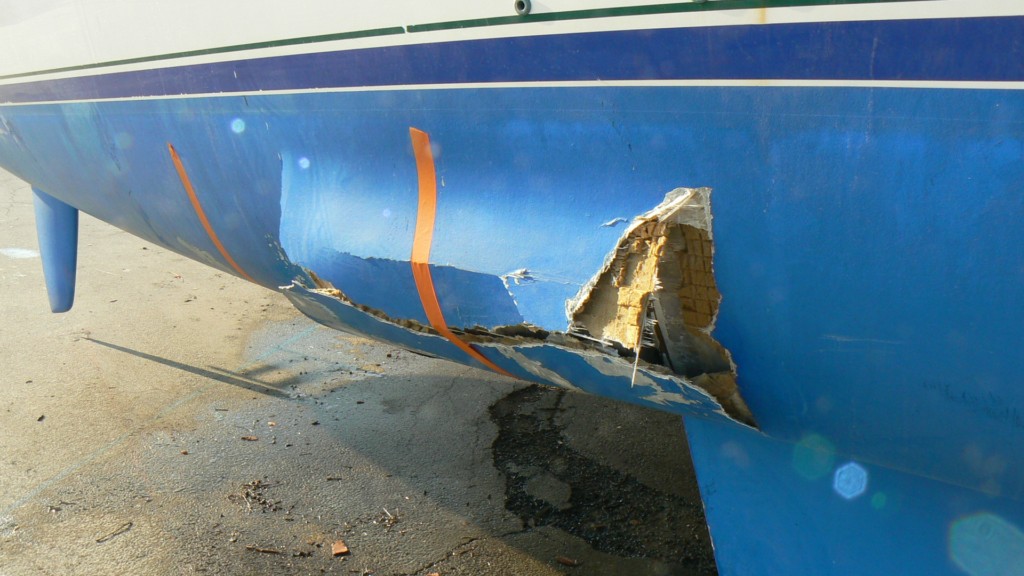
TECHNOLOGICAL INNOVATION
Research and production are going on both for young companies and for big names. One example is nlcomp, established in 2019, that owns the patented rComposite technology, an Eco Friendly Materials alternative to traditional fiberglass. nlcomp replaces thermosetting resins with a thermoplastic matrix, allowing for easy chemical processing and recovery of the raw materials, and enabling the boat to be recycled at the end of its lifecycle.