Tool life is a crucial aspect for every user, as it directly affects production costs, the number of operations that can be performed, and the overall process quality. Several factors determine tool life: wear, mechanical and thermal stresses, and the efficiency of protective coatings.
UFS tackles these challenges with an innovative approach that integrates advanced numerical simulations, such as FEM (Finite Element Method) and CAE (Computer-Aided Engineering), to optimize tool design and ensure longer durability.
Thanks to these simulations, the company can improve the prediction of wear and material fatigue, allowing us to design tools that last longer.
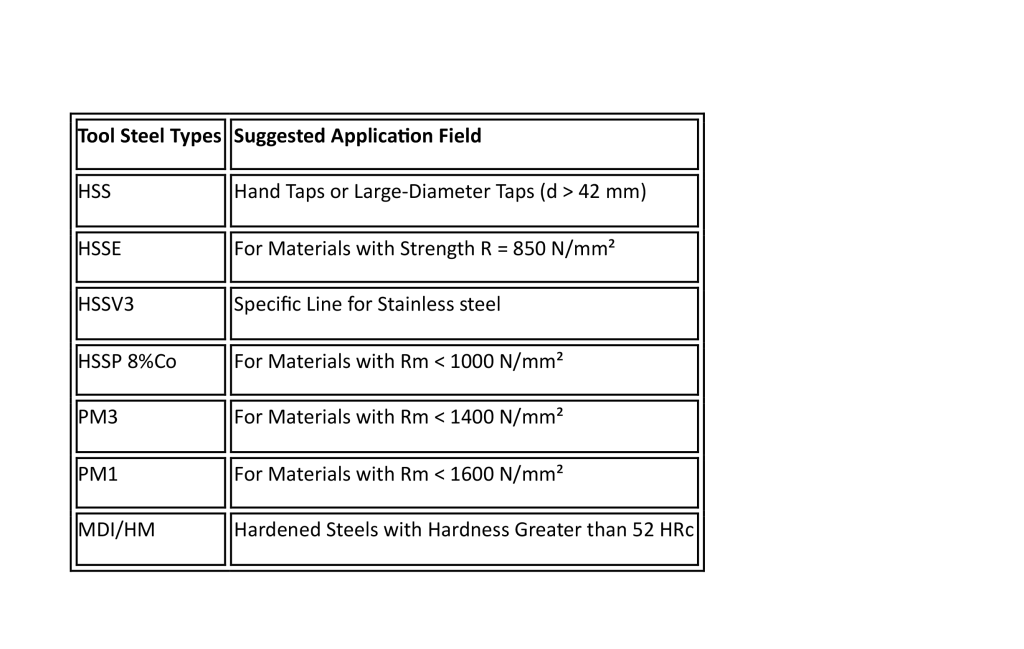
Nonlinear Mechanics in Simulations
A key concept in FEM and CAE simulations is nonlinear mechanics, which models material behavior under extreme conditions, where the response is not proportional to the applied stress. In cutting processes, high forces and deformations lead to nonlinear behaviors that must be accurately predicted.
This approach enables UFS to develop optimized tools for each application, reducing wear and extending operational life.
Material Models and Heat Treatment
UFS employs material models that align with heat treatment processes, a method that enhances the strength and hardness of tools. The accuracy of simulations depends on the ability to derive real models of tempered material behavior, allowing precise predictions of surface hardness and wear resistance. This optimizes tool performance and longevity while reducing production costs.
The Compromise Between Hardness and Toughness
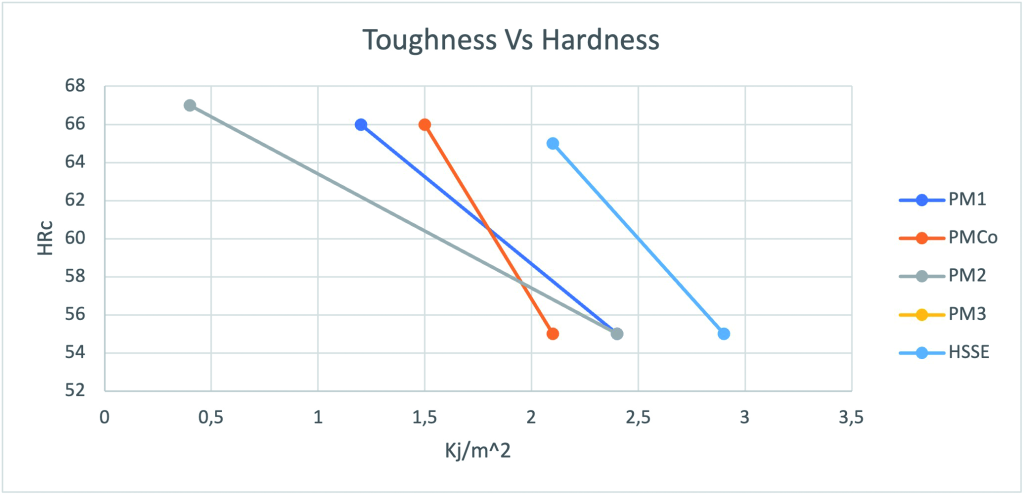
Hardness and toughness are key properties of steels: hardness resists penetration and wear, while toughness allows a material to absorb energy without fracturing.
Tools such as threading taps require high hardness but also toughness to prevent breakage. The optimization of these properties is achieved through heat treatments and the addition of alloying elements such as nickel and molybdenum.
PVD Coatings for Cutting Taps
Cutting taps are coated using PVD (Physical Vapor Deposition) technologies to enhance their durability and efficiency.
Key coatings include:
- TiN: Reduces friction and improves wear resistance.
- TiCN: Increases hardness and reduces the coefficient of friction.
- TxC (DLC): Reduces friction and enhances hardness.
- XP: Improves wear resistance and extends operational life.
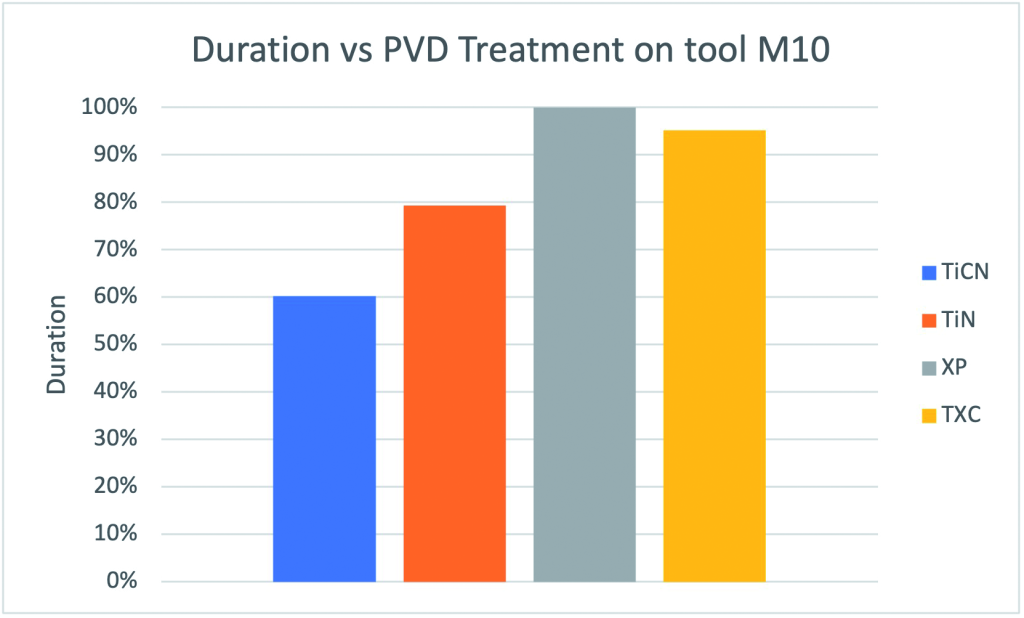
Innovation and Numerical Simulations
UFS’s approach is based on advanced numerical simulations that reduce development times from months to days. The simulations allow to:
- Evaluate the mechanical behavior of tools
- Optimize the design to increase durability
- Improve impact resistance
- Ensure high-strength threads
A significant example is the use of taps with variable hardness, which show a 13% increase in energy absorption capacity and a 10% reduction in internal stresses, improving stability and durability.
Accelerating Time-to-Market
Numerical simulations help reduce the time-to-market of new tools, accelerating the qualification and implementation of innovative processes. This approach allows new products to reach the market in half the time compared to traditional methods.
An Investment that Makes a Difference
Investing in tools designed with advanced simulations brings numerous advantages:
- higher productivity thanks to more durable tools;
- reduction in operational costs due to less wear;
- higher quality in machining.
In a competitive market, choosing UFS taps is a smart strategy that guarantees efficiency, reliability, and innovation.